Draft:MultiFAZE mechanism
Submission declined on 7 August 2024 by Bobby Cohn (talk). This submission seems to be a test edit and not an article worthy of an encyclopedia. Please use the sandbox for any editing tests, but do not submit for review until you have an article that you want reviewed for inclusion in Wikipedia. Thank you.
Where to get help
How to improve a draft
You can also browse Wikipedia:Featured articles and Wikipedia:Good articles to find examples of Wikipedia's best writing on topics similar to your proposed article. Improving your odds of a speedy review To improve your odds of a faster review, tag your draft with relevant WikiProject tags using the button below. This will let reviewers know a new draft has been submitted in their area of interest. For instance, if you wrote about a female astronomer, you would want to add the Biography, Astronomy, and Women scientists tags. Editor resources
| ![]() |
Submission declined on 21 April 2024 by ToadetteEdit (talk). This submission is not adequately supported by reliable sources. Reliable sources are required so that information can be verified. If you need help with referencing, please see Referencing for beginners and Citing sources. Declined by ToadetteEdit 4 months ago. | ![]() |
Submission declined on 5 January 2022 by TheBirdsShedTears (talk). This submission is not adequately supported by reliable sources. Reliable sources are required so that information can be verified. If you need help with referencing, please see Referencing for beginners and Citing sources. Declined by TheBirdsShedTears 2 years ago. | ![]() |
Submission declined on 22 August 2021 by Liance (talk). This draft's references do not show that the subject qualifies for a Wikipedia article. In summary, the draft needs multiple published sources that are: Declined by Liance 3 years ago.
| ![]() |
Comment: I can't find a single source here that mentions find MultiFAZE mechanism? Am I missing something? Theroadislong (talk) 12:03, 12 August 2024 (UTC)
Comment: You say "I intend to tidy it up. Clearly I don't want to put in the work at this point" Clearly you NEED to put the work in for this to be accepted! Theroadislong (talk) 22:00, 10 August 2024 (UTC)
Comment: It is best to convert external links to footnotes. Toadette (Let's talk together!) 13:42, 21 April 2024 (UTC)
Comment: I cannot find a single source that calls this a "MultiFAZE mechanism" besides this article. Q T C 01:37, 29 March 2024 (UTC)
Comment: There are currently 16 refs in this draft, which do not indicate MultiFAZE mechanism. It seems a new compound eccentric mechanism invented by author. TheBirdsShedTears (talk) 07:15, 5 January 2022 (UTC)

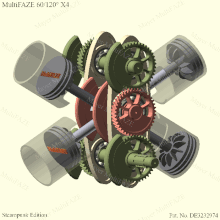
Like the Cardan hypocyclic gear and Archimedes trammel mechanisms, the MultiFAZE (Multiple Fixed-Axis Shaft Compound Eccentric) mechanism converts reciprocating motion to continuous rotary motion and vice versa via elliptical motion. However, it differs from the first two mechanisms in that the rotary shafts (in an engine, the output shafts) have eccentric gears and/or discs rigidly fixed to them, so that power can be transmitted between the contrarotating fixed-axis and orbiting-axis shafts with practically zero relative speed, instead of via a double-speed bearing, to reduce friction and wear. Also, the diameter of the gears is not tied to the stroke of the mechanism, allowing the gears to be made large enough to reduce the loading on the teeth to acceptable levels. There are also fewer constraints on the diameter of the bearings.
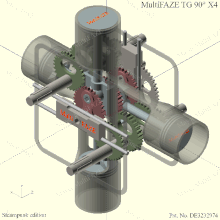
By 1850, it was already known of Cardan gearing (and therefore probably also of the closely related trammel mechanism) that
the fault of this species of parallel motion is that the socket in the centre of the revolving wheel is exposed to a strain equal to twice that on the piston, and which it cannot be conveniently made long enough to resist, so that it is likely to break or speedily shake loose.[1]
Also, more recently:
Early experience demonstrated that the hypocycloidal mechanism was structurally unsuited to transmitting the large forces developed by the piston of a steam engine. But the mechanism had shown its ability to convert linear motion to rotary motion and so found alternative low-load applications such as the drive for printing machines and sewing machines.[2]
The fragile nature of these old mechanisms is the result of the use of a crank on the output shaft with a throw of only 1/4 of the stroke of the mechanism and the leverage effect of the elliptic shaft, doubling the force on the crankpin. Also, the diameter of the hypocyclic gears is tied to the stroke of the mechanism and cannot be made large enough to withstand the forces even in a steam engine.
The MultiFAZE mechanism, however, transmits drive to the output shaft by rotation using eccentric gears. Apart from mass, there are no constraints on the size of the gears, so that their diameter can be increased to reduce the forces acting not only on them, but also on the bearings. Furthermore, the angular speed difference in the contact area is reduced from twice the speed of the individual parts in the case of a crank to zero in the case of gears, reducing friction.
The fixed-axis rotary shafts have eccentric gears and/or discs, the orbital shaft has axial gears and/or discs with eccentric piston pins. Different means are available to ensure the correct alignment and separation of the gears or discs, such as having the elliptic shaft rotate in carriers, which in turn are mounted on eccentric journals on the rotary shafts, giving the carriers a circular motion. At least two fixed-axis rotary shafts are normally required for the carrier and for balance, one of the shafts acting as the main output shaft, while the other(s) can be used to drive auxiliaries.
Potential benefits of a compound eccentric mechanism in an internal combustion engine include perfect balance without additional balance shafts, as the mechanism generates no second-order inertial forces, and the possibility of placing a barrier between the cylinders and the mechanism, allowing the lower part of the cylinders to be put to use. Such a barrier also prevents blow-by of combustion gases into the mechanism and its lubricant and, in the other direction, uncontrolled entry of lubricant into the cylinder and combustion chamber. The pistons no longer require an oil-scraper ring or a skirt and the cylinders are correspondingly shorter.
A rigid double-ended piston-conrod assembly is particularly suitable for 2-stroke operation. In diesel engines, the sinusoidal motion of the pistons has been found to reduce ignition delay, improving efficiency and particularly cold starting.[3][4] As there are no side forces on the pistons, they can be made of ceramic material.[5] An economical MultiFAZE IC engine with adiabatic combustion may have a future beyond that of conventional IC engines.[6]
The Stiller-Smith engine
[edit]

The MultiFAZE mechanism has been used in the Stiller-Smith engine.[7][6][8] The engine has the same cruciform cylinder layout as the Baker-Cross engine[9][10] with two non-articulated, double-ended piston-and-rod assemblies, and uses a MultiFAZE gear train to transmit the motion of the elliptic shaft to two fixed-axis shafts. It dispenses with the carriers of the MultiFAZE mechanism to link the three shafts, the elliptic shaft then consisting only of a spur gear with an eccentric pin on each side. This is referred to by the inventors as an "elliptic trammel" or "floating trammel". However, the eccentric pins are not in the same plane, so that the "trammel" is better described as a crank. The axial offset of the pins, in the absence of other support, give it the characteristics of a cantilever. This cantilever crank floats between two perpendicular reciprocating piston rods, alternately supporting one rod and being supported by the other.
This means that, when a piston pair passes through its dead-centre points, its central bearing is exposed to a moment which is the product of its momentum and the dimensions of the cantilever, while the other piston pair (in its mid-position) turns about its axis. The floating cantilever crank wobbles and the pistons overshoot. Bearings and gear teeth are unevenly loaded. In a two-stroke engine, this situation is mitigated over a narrow band of operating conditions by the gas pressure forces. The use of flexible connecting rods has been considered.[6][11] If the floating trammel wobbles, the gear teeth are similarly unevenly loaded.
As the angle between the line of action of the eccentric and orbital gears and the actual direction of movement of the teeth in the contact area varies cyclically,[12] the absence of carriers requires an additional external train of gears to synchronise the shafts and ensure continuous engagement of the gears and uninterrupted power transmission.
These and other issues have provided material for theoretical analyses and computer models in some 30 technical reports, conference papers and articles[13] over a number of years. An article on a popular news website reported that the engine produced 150 horsepower for a weight of 100 pounds and that it was "really unique".[8] A thumbnail image shows a 4-cylinder cruciform engine with 2-stroke features.[14]
While dispensing with the carriers undoubtedly saves weight, supporting the orbital shaft in the connecting rods invites wobble and enlargement of the orbit, increasing piston stroke and altering port timing, depending on the operating conditions, and imposing bending loads on the connecting rods. Lateral forces on the pistons can be reduced by supporting the rods in linear bearings.[15] However, the gears and bearings remain exposed to irregular forces with high local stress concentrations associated with the cantilever properties of the "floating trammel".
These problems could theoretically be avoided by mounting the reciprocating pins rigidly on the connecting rods and having them engage bearings in the gearwheel.[16] The bearings would then be in the same plane, which would eliminate the cantilever, but this would limit the diameter of the bearings to less than half the piston stroke. Compound eccentric engine designs tend to have a short stroke/large piston area configuration, which places a high load on the bearings.
Two prototype engines have been built[17] and further versions with 8, 12, 16 and more cylinders have been proposed. Perfect balance without counterweights and with equal cylinder spacing in each block can be obtained in a Stiller-Smith-type engine with 16 cylinders,[18] using the same balancing principle as a straight-4 engine with a single-plane crankshaft.
Exploitation, benefits gained
[edit]The MultiFAZE mechanism with a floating cantilever crank (see two animations above) was the subject of Prof. Smith's PhD thesis[7] and became known as the Stiller-Smith mechanism.
Numerous patents were issued for the mechanism in the US and other countries citing Stiller and Smith as the inventors, without reference to the original patent.
Virtually every newspaper in West Virginia, USA and the wider region published articles on the new ‘Stiller-Smith Engine’.
West Virginia University College of Engineering received its first million dollar grant for research on the mechanism allowing it to hire extra staff and furnish all the offices with carpets. The programme lasted three years and boosted the position of the mechanical engineering department. The University recognised the need for an intellectual property policy and set up the WVU Technology Transfer Center and later the Research Corporation. Stiller was eventually recognized as one of West Virginia’s outstanding inventors.[19]
As a prolific inventor, Dr. Stiller was recognised as the State Inventor by the Governor of West Virginia, earning a spot in the Inventors Hall of Fame in Akron, Ohio. As an alumnus of MMI Preparatory School, he was inducted into the Wall of Fame there in 2018.[20]
Prof. Smith was elected Lifetime Fellow of the National Academy of Inventors in 2016 for numerous inventions including the modified MultiFAZE mechanism.[21]
The US Congress awarded a grant of $1,760,000 to the Army for research on the Stiller-Smith reciprocating engine to explore its use for future combat vehicles.[22]
Intellectual property/prior art
[edit]Dearing's ellipsograph of 1927 uses a pair of spur gears in conjunction with a parallelogram frame. A train of three gears would have stabilised the parallelogram in the end positions, and would have made it a MultiFAZE mechanism.
Fowler's ellipsograph of 1952 uses a pair of spur gear rings in conjunction with fixed perpendicular guides. However, this is an inversion of the scotch yoke and not the MultiFAZE principle.
Patent No. DE3232974 filed in 1982 discloses various embodiments of the MultiFAZE mechanism, including one for an engine with a 4-cylinder cruciform layout. The application was initially published on 15 March 1984.
Prof. Stiller, a chemist at West Virginia University, relates that, in the early 1980's, he was given a so-called do-nothing machine, a toy version of the Archimedes trammel which he claimed gave him the idea for what was to become the Stiller-Smith engine.[19] However, this does not explain how he made the inventive step to arrive at the eccentric gear train that is the novel feature of the MultiFAZE mechanism.
On 06 July 1984, US patent application Serial No. 628248 was filed by West Virginia University for a MultiFAZE mechanism with a floating cantilever crank, which provided the priority for further applications filed a year later in Japan and South Korea. The US application was later abandoned, the Korean application was refused and discontinued in 1993 and there is no bibliographic data for the Japanese application beyond the initial publication stage. Successful applications in the USA (US4641611, US4682569, US5046459) and numerous other countries around the world followed, with Profs. James E. Smith and Alfred H. Stiller given as the inventors of the mechanism.
References
[edit]- ^ James White's steam engine of 1801 in Appleton's Dictionary of Machines, Mechanics, Engine-work, and Engineering Google Books, p. 490
- ^ White, G. (1988), "Epicyclic gears applied to early steam engines", Mechanism and Machine Theory, 23 (1): 25–37, doi:10.1016/0094-114X(88)90006-7
- ^ Combustion ignition delay in engines with unconventional piston motions (full text not available 130123), Craven, K K, Smith, J E, Clark, N N
- ^ Piston Motion and Ignition Delay: Details on Coal-Based Fuel Injection and Effects of Mass Leakage, SAE Technical Paper 900388, 1990, Craven, K K, Smith, J E, Clark, N N
- ^ Thermodynamic implications of the Stiller-Smith mechanism (abstract), Lee, K; Clark, N; George, A; Petrucci, V West Virginia Univ.
- ^ a b c Clean engines - A combination of advanced materials and a new engine design, James E. Smith, Randolph A. Churchill, Jacky Prucz, West Virginia University
- ^ a b The dynamic analysis of an elliptical trammel mechanism for possible application to an internal combustion engine with a floating crank, James E. Smith, PhD thesis, 1984, Department of Mechanical and Aerospace Engineering, West Virginia University.
- ^ a b WVU professors design 'revolutionary' engine, UPI Archives Nov. 5, 1984 (malware warning encountered 16/02/2022, found OK again 26/03/2022)
- ^ Four-cylinder, Four-cycle Engine With Two Reciprocating Components, A.J.S Baker, M.E Cross, The Institution of Mechanical Engineeers, Automobile Division, Volume 188 38/74
- ^ Baker-Cross engine US Patent No. 3977303
- ^ Multimodeling strategy for assessment of complex mechanical systems (abstract), W.G.WangV.H.MucinoJ.E.SmithN.T.Sivaneri
- ^ Design Loads of the Floating Gear System in the Stiller-Smith Mechanism (abstract) James E. Smith, Victor Mucino, Nithi T. Sivaner
- ^ List of technical papers (ResearchGate, available against payment)
- ^ Photo 2T (no longer available)
- ^ High-load, squeeze action linear bearings with beam deflection (abstract), N.Clark, J.E.Smith, J.Smith, R.Craven
- ^ The Stiller-Smith Engine: Floating Gear Analysis (abstract), Craven, R., Smith, J., Butler, S., West Virginia Univ.
- ^ The Stiller-Smith Engine-The Dewelopment of a New Environment for High-Tech Materials (abstract), James E. Smith, Robert Craven, Randolph Churchill
- ^ Complete Balancing of the Stiller-Smith Engine: 4,8,12,16 or More Cylinders (full text), CRAVEN R (West Virginia Univ., WV, SMITH J E (West Virginia Univ., WV)
- ^ a b Chemical Engineering at West Virginia University:A Living History, p. 79
- ^ MMI Prepratory School inducts Wall of Fame members https://www.timesleader.com/features/715123/mmi-prepratory-school-inducts-wall-of-fame-members
- ^ National Academy of Inventors https://academyofinventors.org/search-fellows/
- ^ November 13, 1989 CONGRESSIONAL RECORD—HOUSE Vol. 135 Part 20 P. 28453 https://archive.org/details/sim_congressional-record-proceedings-and-debates_november-08-15-1989_135-redacted/page/28452/mode/2up?q=%22stiller-smith%22&view=theater
See also
[edit]Wheelchair propulsive mechanism
Rotation to translation mechanism