Two-stroke engine: Difference between revisions
m Reverted edits by 205.202.240.144 (talk) to last revision by Vipinhari (HG) |
No edit summary |
||
Line 21: | Line 21: | ||
Although the principles remain the same, the mechanical details of various two-stroke engines differ depending on the type. The design types of the two-stroke engine vary according to the method of introducing the charge to the cylinder, the method of scavenging the [[cylinder (engine)|cylinder]] (exchanging burnt exhaust for fresh mixture) and the method of exhausting the cylinder. |
Although the principles remain the same, the mechanical details of various two-stroke engines differ depending on the type. The design types of the two-stroke engine vary according to the method of introducing the charge to the cylinder, the method of scavenging the [[cylinder (engine)|cylinder]] (exchanging burnt exhaust for fresh mixture) and the method of exhausting the cylinder. |
||
=== |
===Pie controlled inlet port=== |
||
[[Piston]] port is the simplest of the designs. All functions are controlled solely by the piston covering and uncovering the ports as it moves up and down in the cylinder. A fundamental difference from typical four-stroke engines is that the [[crankcase]] is sealed and forms part of the induction process in gasoline and [[hot bulb engine]]s. Diesel engines have mostly a [[roots blower]] or piston pump for scavenging. |
[[Piston]] port is the simplest of the designs. All functions are controlled solely by the piston covering and uncovering the ports as it moves up and down in the cylinder. A fundamental difference from typical four-stroke engines is that the [[crankcase]] is sealed and forms part of the induction process in gasoline and [[hot bulb engine]]s. Diesel engines have mostly a [[roots blower]] or piston pump for scavenging. |
||
Revision as of 18:39, 14 May 2010
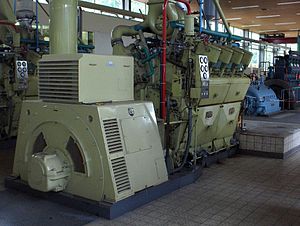
A two-stroke engine is an internal combustion engine that completes the thermodynamic cycle in two movements of the piston (compared to twice that number for a four-stroke engine). This increased efficiency is accomplished by using the beginning of the compression stroke and the end of the combustion stroke to perform simultaneously the intake and exhaust (or scavenging) functions. In this way two-stroke engines often provide strikingly high specific power. Gasoline (spark ignition) versions are particularly useful in lightweight (portable) applications such as chainsaws and the concept is also used in diesel compression ignition engines in large and non-weight sensitive applications such as ships and locomotives.
Invention of the two-stroke cycle is attributed to Scottish engineer Dugald Clerk who in 1881 patented his design, his engine having a separate charging cylinder. The crankcase-scavenged engine, employing the area below the piston as a charging pump, is generally credited to Englishman Joseph Day (and Frederick Cock for the piston-controlled inlet port).
Applications
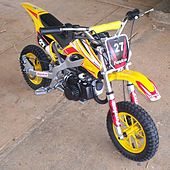
The two-stroke engine was most popular throughout the 20th century in motorcycles, small engined devices such as chainsaws and outboard motors and some cars. This was due to their simple design (and resulting low cost) and higher power-to-weight ratios. Most designs used total-loss lubrication, with the oil being burnt in the combustion chamber, causing "blue smoke" and other types of exhaust pollution. This is the major reason for two-stroke engines being replaced with four-stroke engines in most applications. Two-stroke engines are commonly used in high-power, handheld applications such as string trimmers and chainsaws. The light overall weight, and light-weight spinning parts give important operational and even safety advantages. Only a two-stroke running on a gasoline-oil mixture can power a chainsaw running in any position.
These engines are still used for small, portable, or specialized machine applications such as outboard motors, high-performance, small-capacity motorcycles, mopeds, underbones, scooters, tuk-tuks, snowmobiles, karts, ultralights, model airplanes (and other model vehicles) and lawnmowers. The two-stroke cycle is used in many diesel engines, most notably large industrial and marine engines, as well as some trucks and heavy machinery.
A number of mainstream automobile manufacturers have used two-stroke engines in the past, including the Swedish Saab and German manufacturers DKW and Auto-Union. The Japanese manufacturer Suzuki did the same in the 1970s.[1] Production of two-stroke cars ended in the 1980s in the West, but Eastern Bloc countries continued until around 1991, with the Trabant and Wartburg in East Germany and Syrena[citation needed] in Poland. Lotus of Norfolk, UK, has a prototype direct-injection two-stroke engine intended for alcohol fuels called the Omnivore[2][3] which it is demonstrating in a version of the Exige.[4]
Different two-stroke design types
Although the principles remain the same, the mechanical details of various two-stroke engines differ depending on the type. The design types of the two-stroke engine vary according to the method of introducing the charge to the cylinder, the method of scavenging the cylinder (exchanging burnt exhaust for fresh mixture) and the method of exhausting the cylinder.
Pie controlled inlet port
Piston port is the simplest of the designs. All functions are controlled solely by the piston covering and uncovering the ports as it moves up and down in the cylinder. A fundamental difference from typical four-stroke engines is that the crankcase is sealed and forms part of the induction process in gasoline and hot bulb engines. Diesel engines have mostly a roots blower or piston pump for scavenging.
Reed inlet valve
The reed valve is a simple but highly effective form of check valve commonly fitted in the intake tract of the piston-controlled port. They allow asymmetric intake of the fuel-charge, improving power and economy, while widening the power band. They are widely used in ATVs, and marine outboard engines.
Rotary inlet valve
The intake pathway is opened and closed by a rotating member. A familiar type sometimes seen on small motorcycles is a slotted disk attached to the crankshaft which covers and uncovers an opening in the end of the crankcase, allowing charge to enter during one portion of the cycle.
Another form of rotary inlet valve used on two-stroke engines employs two cylindrical members with suitable cutouts arranged to rotate one within the other - the inlet pipe having passage to the crankcase only when the two cutouts coincide. The crankshaft itself may form one of the members, as in most Glowplug model engines. In another embodiment, the crank disc is arranged to be a close-clearance fit in the crankcase and is provided with a cutout which lines up with an inlet passage in the crankcase wall at the appropriate time, as in the Vespa motor scooter.
The advantage of a rotary valve is that it enables the two-stroke engine's intake timing to be asymmetrical which is not possible with two-stroke piston port type engines. The two-stroke piston port type engine's intake timing opens and closes before and after top dead center at the same crank angle making it symmetrical whereas the rotary valve allows the opening to begin earlier and close earlier.
Rotary valve engines can be tailored to deliver power over a wider speed range or higher power over a narrower speed range than either piston port or reed valve engine. Where a portion of the rotary-valve is a portion of the crankcase itself it is particularly important that no wear is allowed to take place.
Crossflow-scavenged
In a crossflow engine the transfer ports and exhaust ports are on opposite sides of the cylinder and a deflector on the top of the piston directs the fresh intake charge into the upper part of the cylinder pushing the residual exhaust gas down the other side of the deflector and out of the exhaust port. The deflector increases piston's weight and its exposed surface area, and also makes it difficult to achieve an efficient combustion chamber shape. This design has been largely superseded by loop scavenging method (below), although for smaller or slower engines the crossflow-scavenged design can be an acceptable approach.
Loop-scavenged

1=TDC
2=BDC
A: wash
B: Exhaust
C: Compression
D: Power
This method of scavenging uses carefully shaped and positioned transfer ports to direct the flow of fresh mixture toward the combustion chamber as it enters the cylinder. The fuel/air mixture strikes the cylinder head then follows the curvature of the combustion chamber then is deflected downward. This not only prevents the fuel/air mixture traveling directly out the exhaust port but creates a swirling turbulence which improves combustion efficiency, power and economy. Usually a piston deflector is not required, so this approach has a distinct advantage over the cross flow scheme (above). Often referred to as "Schnuerle" (or "Schnürl") loop scavenging after the German inventor of an early form in the mid 1920s, it became widely adopted in that country during the 1930s and spread further afield after World War II. Loop scavenging is the most common type of fuel/air mixture transfer used on modern two stroke engines. Suzuki was one of the first manufacturers outside of Europe to adopt loop scavenged two stroke engines. This operational feature was used in conjunction with the expansion chamber exhaust developed by German motorcycle manufacturer, MZ and Walter Kaaden. Loop scavenging, disc valves and expansion chambers worked in a highly coordinated way that saw a significant increase in the power output of two-stroke engines, particularly from the Japanese manufacturers Suzuki, Yamaha and Kawasaki. Suzuki and Yamaha enjoyed success in grand Prix motorcycle racing in the 1960s due in no small way to the increased power afforded by loop scavenging. An additional benefit of loop scavenging was that the piston could be made nearly flat or slightly dome shaped. This enabled the piston to be appreciably lighter and stronger and consequently tolerated higher engine speeds. The "flat top" piston also has better thermal properties and is less prone to uneven heating, expansion, piston seizures, dimensional changes and compression losses.
Uniflow-scavenged

1=TDC
2=BDC
A: wash
B: Exhaust
C: Compression
D: Power
In a uniflow engine the mixture, or air in the case of a diesel, enters at one end of the cylinder controlled by the piston and the exhaust exits at the other end controlled by an exhaust valve or piston. The scavenging gas-flow is therefore in one direction only, hence the name uniflow. The valved arrangement is common in diesel locomotives (Electro-Motive Diesel) and large marine two-stroke engines (Wärtsilä). Ported types are represented by the opposed piston design in which there are two pistons in each cylinder, working in opposite directions such as the Junkers Jumo and Napier Deltic.[5] The once-popular split-single design falls into this class being effectively a folded uniflow. With advanced angle exhaust timing uniflow engines can be supercharged with a crankshaft driven (piston [6] or Roots) blower.
In Japan. Nissan Diesel Motor was manufacturing Uniflow_Two-stroke_Diesel_Engine(ja:ユニフロー掃気ディーゼルエンジン) from General Motors from under a license of Detroit Diesel Series 71.
The latest invention, called the Reversed Uniflow two-stroke engine, has a large intake valve for compressed intake air without fuel-oil mixture. Direct fuel injection is to be used for gasoline or diesel fuel, pending intake air pressure. This engine will work on the Miller cycle. US Patent #6889636.
Stepped piston engine
The piston of this engine is "top-hat" shaped, the upper section forming the regular cylinder. and the lower section performing a scavenging function. The units run in pairs, the lower half of one piston charging an adjacent combustion chamber.
This system is still partially dependent on total loss lubrication (for the upper part of the piston), the other parts being sump lubricated with cleanliness and reliability benefits. The piston weight is only about 20% heavier than a loop-scavenged piston because skirt thicknesses can be less. The patents on this design are held by Bernard Hooper Engineering Ltd (BHE).[7]
Power valve systems
Many modern two-stroke engines employ a power valve system. The valves are normally in or around the exhaust ports. They work in one of two ways: either they alter the exhaust port by closing off the top part of the port which alters port timing such as Ski-doo R.A.V.E, Yamaha YPVS, Honda RC-Valve, Cagiva C.T.S., Suzuki AETC system or by altering the volume of the exhaust which changes the resonant frequency of the expansion chamber, such as Honda V-TACS system. The result is an engine with better low-speed power without sacrificing high-speed power.
Direct injection
Direct injection has considerable advantages in two-stroke engines, eliminating some of the waste and pollution caused by carbureted two-strokes where a proportion of the fuel/air mixture entering the cylinder goes directly out, unburned, through the exhaust port. Two systems are in use, low-pressure air-assisted injection, and high pressure injection.
Two-stroke diesel engines
Diesel engines rely solely on the heat of compression for ignition (unlike gasoline engines, which employ a spark plug). Intake is via piston-controlled Schnuerle porting but combustion gases can exit through conventional exhaust valves located in the cylinder head or through piston porting just above bottom dead center (BDC). Modern two-stroke diesels are all scavenged by forced induction, most usually with a mechanically driven Roots blower. When extra power is required a form of hybrid turbocharger will be used, with the exhaust-driven components taking over at higher speed.
Marine two-stroke diesel engines directly coupled to the propeller are able to start and run in either direction as required. The fuel injection and valve timing is mechanically readjusted by using a different set of cams on the camshaft. Thus the engine can be run in reverse to move the vessel backwards.
Lubrication
The common two-stroke engines that consumers regularly come across (such as motorcycles and power tools) cannot use regular sump lubrication, since the crankcase is being used to pump fuel-air mixture into the cylinder. Traditionally, all moving parts of the engine itself (big-ends, little-ends, main-bearings, and piston/ring assemblies) were lubricated by a pre-mixed fuel-oil mixture (at a ratio between 16:1 and 50:1). Increasingly, even small two-stroke engines have pumped lubrication from a separate tank of oil. This is still a total-loss system with the oil being burnt the same as in the older system, but at a lower and more economical rate. It is also cleaner, reducing the problem of oil-fouling of the spark-plugs and coke formation in the cylinder and the exhaust. These pumped systems would be difficult to implement in hand-held two-stroke devices such as chainsaws (which must operate in any attitude) and up to the present time such motors still run on fuel-oil mixture.
All two-stroke engines running on a petroil mix will suffer oil-starvation if forced to turn at speed with the throttle closed, e.g. motorcycles descending long hills and perhaps when decelerating gradually from high-speed by changing down through the gears. Two-stroke cars (such as those that were popular in Eastern Europe in mid-20th century) were in particular danger and were usually fitted with freewheel mechanisms in the powertrain, allowing the engine to idle when the throttle was closed, requiring the use of the brakes in all slowing down situations.
Two-stroke diesel engines use a wet sump lubrication system, as they are scavenged by fresh compressed air thus not relying on crankcase compression of the combustible mixture.
Two-stroke reversibility
To understand this discussion, it is convenient to think in motorcycle terms, where the exhaust pipe faces into the cooling air stream, and the crankshaft commonly spins in the same axis and (in almost all cases) direction as do the wheels i.e. "forwards". Some of the considerations discussed here apply to four-stroke engines (which cannot reverse their direction of rotation without fairly major modification) almost all of which spin forwards too.
Regular gasoline two-stroke engines will run backwards for short periods and under light load with little problem, and this has been used to provide a reversing facility in microcars such as the Messerschmitt KR200 that lacked reverse gearing. Where the vehicle has electric starting, the motor will be turned off and re-started backwards by turning the key in the opposite direction. The old flywheel magnetos work normally in reverse because the cam controlling the points is symmetrical, breaking contact before TDC equally well whether running forwards or backwards. Two-stroke golf carts used a similar type of system and would often use the same reversing switch as an electric cart. Reed-valve engines will run backwards just as well as piston-controlled porting, though rotary valve engine have asymmetrical inlet timing and will not run very well.
Mercury Marine's Mark 75 and Mark 78 gasoline outboard motors, built from 1957 to 1960, used this system, which they called "direct reversing."[citation needed]
Model airplane engines with reed-valves can be mounted in either tractor or pusher configuration without needing to change the propeller. These motors are compression ignition, so there are no ignition timing issue and no difference between running forwards and running backwards.
There are serious disadvantages to running any engine backwards under load for any length of time, and some of these reasons are general, applying equally to both two-stroke and four-stroke engines. Most disadvantages are intrinsic, unavoidable even in the case of a complete re-design. The problem comes about because in "forwards" running the major thrust face of the piston is on the back face of the cylinder which, in a two-stroke particularly, is the coolest and best lubricated part. The forward face of the piston is less well-suited to be the major thrust face since it covers and uncovers the exhaust port in the cylinder, the hottest part of the engine, where piston lubrication is at its most marginal. The front face of the piston is also more vulnerable since the exhaust port, the largest in the engine, is in the front wall of the cylinder. Piston skirts and rings risk being extruded into this port, so it is always better to have them pressing hardest on the back wall (where there are only the transfer ports) and there is good support. In some engines, the small end is offset to reduce thrust in the intended rotational direction and the forward face of the piston has been made thinner and lighter to compensate - but when running backwards, this weaker forward face suffers increased mechanical stress it was not designed to resist.[8]
In addition, two-stroke oil pumps may not work in reverse, in which case the engine will suffer oil starvation within a short time. Running a motorcycle engine backwards is relatively easy to initiate and in rare cases can be triggered by a back-fire. However, it is not advisable.
Some engines, such as certain Rotax racing engines, have been designed with the exhaust port on the major thrust side. Piston design was adjusted accordingly and they appear to run reliably.[citation needed]
Certain large two-stroke ship diesels are reversible. Like four-stroke ship engines (some of which are also reversible) they use mechanically operated valves and so require additional camshaft mechanisms.[citation needed]
See also
- Bourke Engine
- Junkers Jumo 205
- Napier Deltic
- Twingle engine
- Wärtsilä-Sulzer RTA96-C
- Kadenacy effect
- Four-stroke
References
- ^ Suzuki LJ50 INFO
- ^ Green Car Congress: Lotus, QUB and Jaguar to Develop Variable Compression Ratio, 2-Stroke OMNIVORE Research Engine
- ^ Lotus Engineering Omnivore Variable Compression Ratio Engine to Debut in Geneva
- ^ Lotus developing efficient two-stroke OMNIVORE engine - Autoblog
- ^ "junkers". Iet.aau.dk. Retrieved 2009-06-06.
- ^ Junkers truck engine 1933.
- ^ Template:BHE Stepped Piston Engine
- ^ Ross and Ungar, "On Piston Slap as a Source of Engine Noise," ASME Paper
External links
- How Stuff Works: Two-Stroke Engine
- Sherman, Don (December 17, 2009), "A Two-Stroke Revival, Without the Blue Haze", New York Times.